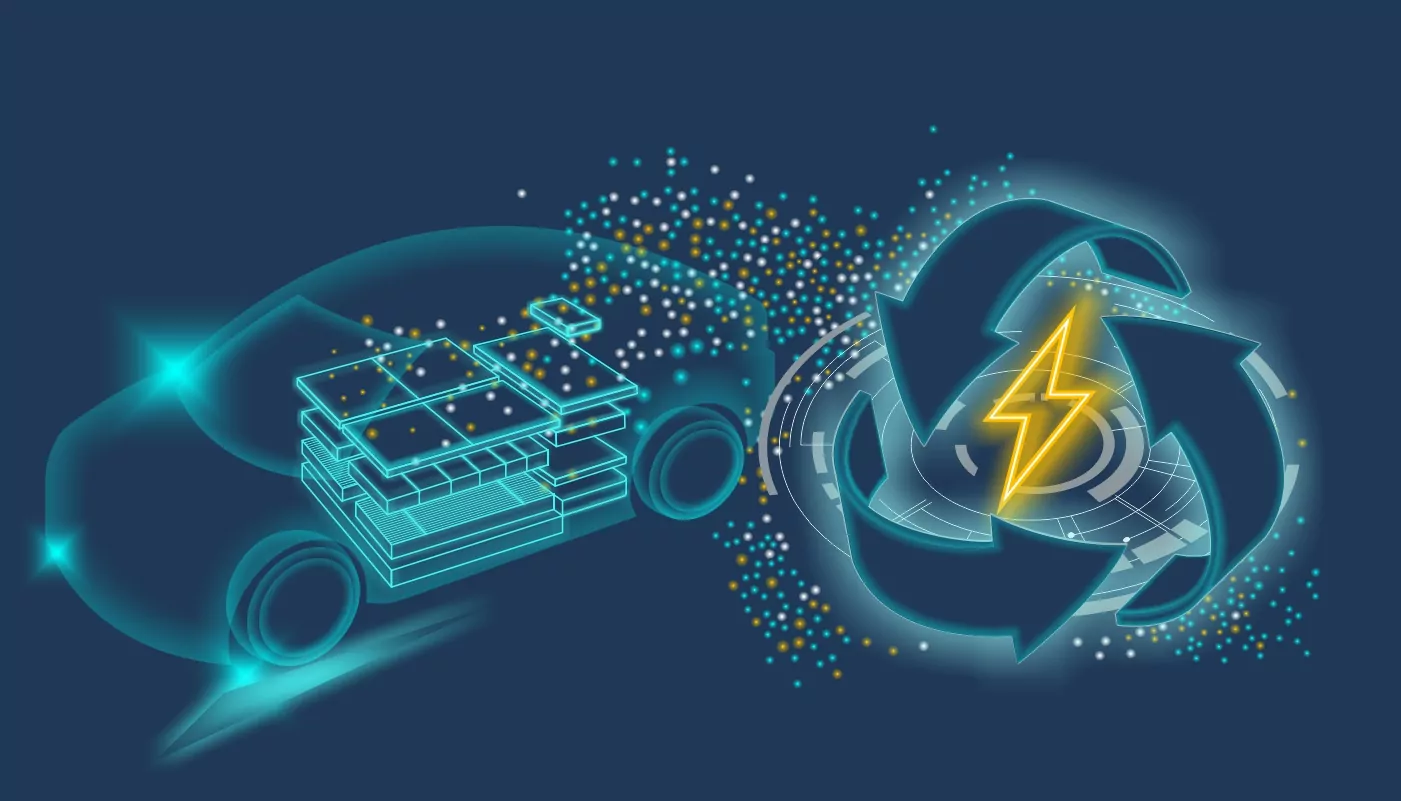
氢化
高效率传质和热传递
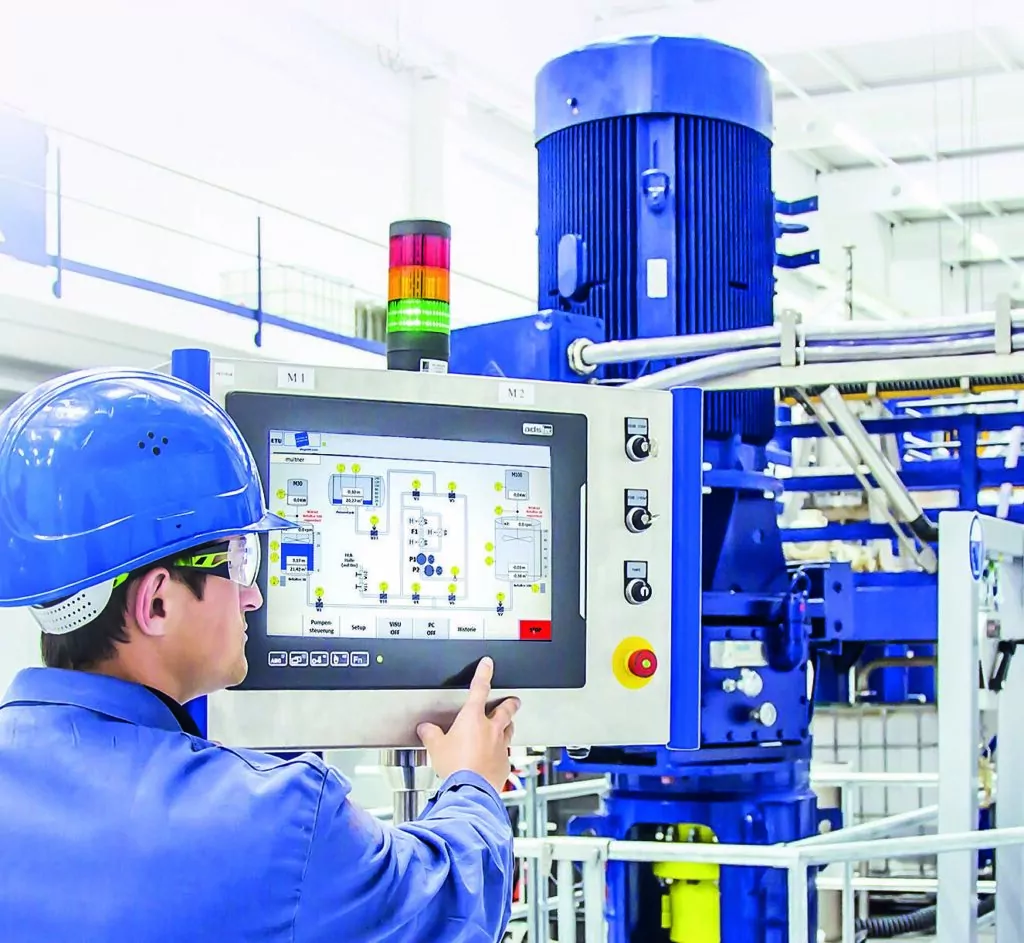
搅拌系统主要有以下任务
- 加强氢气从气相到液相的传质
- 通过逆着反应器中的换热器流动来去除反应热
- 催化剂悬浮
- 均化反应器内物料
- 避免浓度和温度差
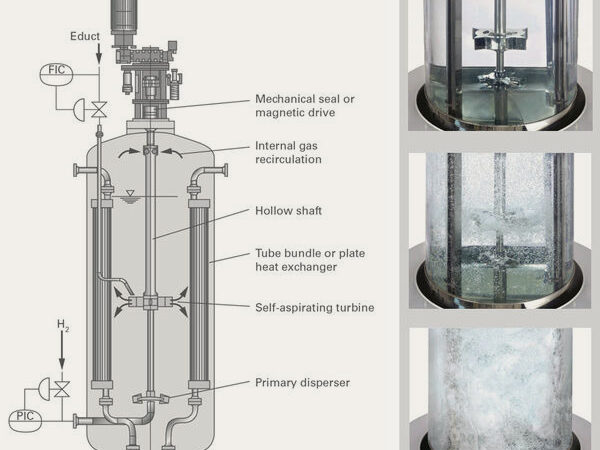
特殊化学品加氢装置
一家涂料行业特种化学品制造商通过在德国 Schopfheim 的 EKATO 加氢试验工厂的测试确定,可以将催化剂负载量从 2.5% 减少到 1.0%,将反应时间从 4 减少到 2 小时,如果氢气的分散和反应器的冷却能力得到改善。 现有加氢反应器的后续改造由 EKATO 在工艺工程和机械方面规划和执行。 改造的核心要素是将有效容积为 2 立方米的反应器转换为独特的 EKATO 组合气体,以及对现有冷却系统的优化。 每年启动 1200 次,每年可节省 3,600 公斤 Pd/C 催化剂,从而节省约 每年 400,000.00 欧元。
与 EKATO 一起成功优化加氢反应器
- 年节省 3,600 kg Pd/C 催化剂
- 每年节省约 400,000€ 欧元
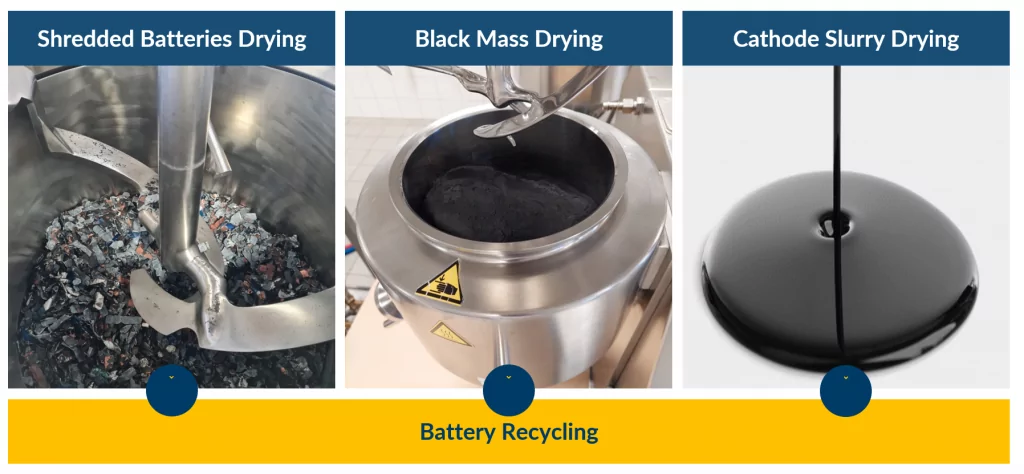
活性药物成分 (API) 的生产
我们新加氢装置的预装合格模块在到货当天安装,并于同月开始生产
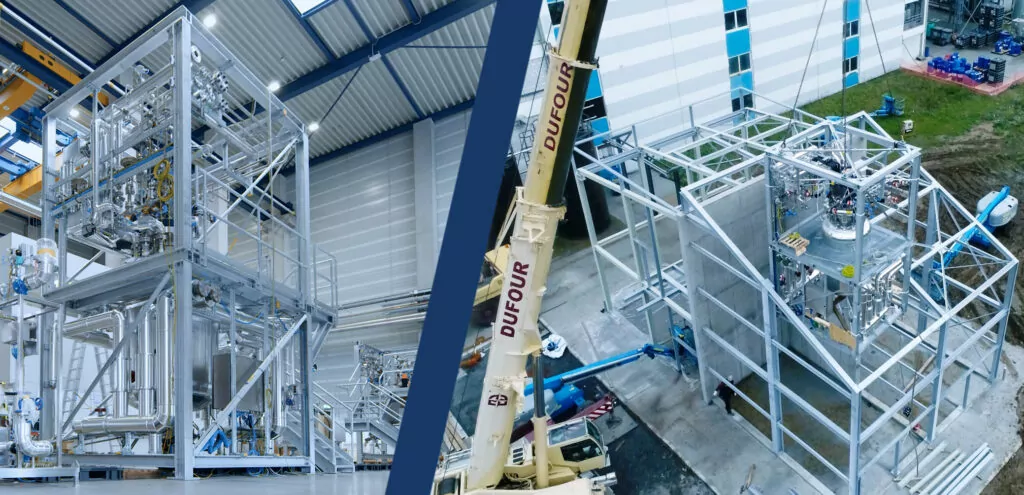
糖醇加氢装置
山梨糖醇是通过葡萄糖氢化获得的糖醇。糖醇在食品工业中用作糖替代品,也是许多其他应用和市场的重要原材料。为了在经济效率要求不断提高的情况下确保最佳产品质量,EKATO 进行了广泛的开发研究,以分析和优化糖类氢化为山梨糖醇、木糖醇和甘露糖醇等糖醇的过程。这些开发研究的目的是提高时空产率,最大限度地减少残留还原糖的含量,抑制葡萄糖酸的形成,并提高催化剂寿命。
基于这些广泛的研究,开发了一种新的、优化的标准系列氢化反应器,用于生产加料体积高达 88 m3 的糖醇。除了工艺工程优化外,还通过 FEM 研究了新的反应器系列,以排除在循环载荷下反应器内部构件失效的可能性。
极具竞争力的多元醇衍生物加氢技术
- 高性能反应器技术
- 坚固和可靠的设备
- 低投资资本支出
- 低运营费用
盘管的模态分析 FEA 可以模拟激励频率的影响。 结果有助于通过优化设计,防止疲劳失效
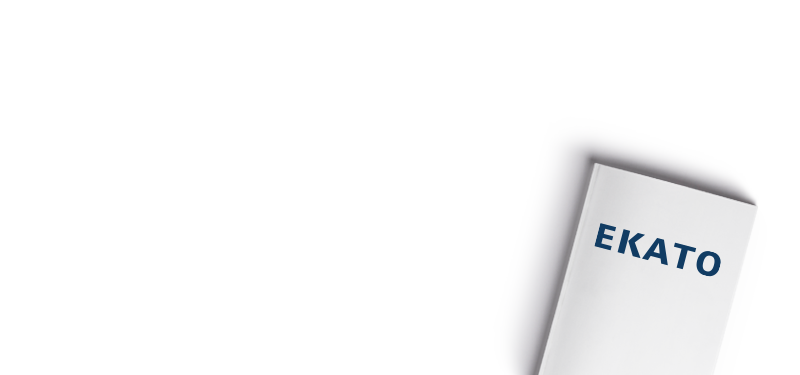